Sourced from: http://feedproxy.google.com/~r/RamblingRenovators/~3/zeeYhCDxdCw/how-to-design-room-step-by-step-easy.html
Week 3 of the One Room Challenge has started off with lots of great progress! Last week, I talked about the importance of
starting any home remodel project with a plan. Let me show you how far along we’ve come with that plan and walk you through the next element:
How to design a room step by step
. Not only that, but I’m going to share how you can
design a room online for free using free online apps and design software
.
Designing a room might seem difficult but I think it’s something anyone can do. Read on for the 4 exact and easy steps I use, from where to begin to decorate a room, the room layout apps I use, and the order in which I decorate.
Welcome and thanks for stopping by! If you’re new here, I’m a Toronto-based blogger and plaid enthusiast who mixes DIY with traditional design. Catch up on Week 1 and Week 2 of this guest bedroom remodel.
The room is looking fresh and bright. Here’s what we’ve done so far:
- demolition of old closet and removal of old trim
- installation of new closet system
- reframing of closet door
- installation of bifold doors
- installation of door and window trim and baseboards
- painting walls and ceiling
The walls are Paper White OC-55 from Benjamin Moore. It is a cool soft white with just the slightest hint of grey. Because we have a cove ceiling here, I knew I wanted to paint the walls and ceiling all the same colour to make that architectural feature disappear. The room isn’t that large so having everything in one shade of paint would make the room feel much more expansive.
Here’s what the room looked like Before. I don’t miss those red walls at all. Not one bit. Now, the sunlight bounces around the room and gives the room that calm and peaceful feeling I wanted this guest bedroom to have.
So let’s dive deeper into that feeling… how did I decide what I wanted this room to look like? How did I design this room in 3D? What free tools and process did I use and how can YOU be your own designer?
How To Design A Room Step By Step
The first step to designing a room is assessing what you have to work with. That begins with a floor plan.
1. Create a Floor Plan of the Current Room
I create two plans:
- a rough hand-written version showing all the room dimensions and location of windows, doors, and other architectural elements. You can use my FREE Download: Current State Checklist found here which contains grid paper for this task.
- take that rough sketch and translate it into a digital floor plan. For this, I like to use Urban Barn’s Room Planner, a FREE online room planning tool. This is my favourite app to design a room layout for free. With this tool, I can create the room and then place and move furniture around until I settle on a design I like. Note: Though this tool is built to work with the furniture Urban Barn sells, you can create “generic” furniture and alter the dimensions to match any current pieces in your own home, or match any new furniture you’re considering purchasing. You can even change colours and patterns to give you a more realistic visual layout.
Here’s the empty floor plan of our guest bedroom I created in the Room Planner:
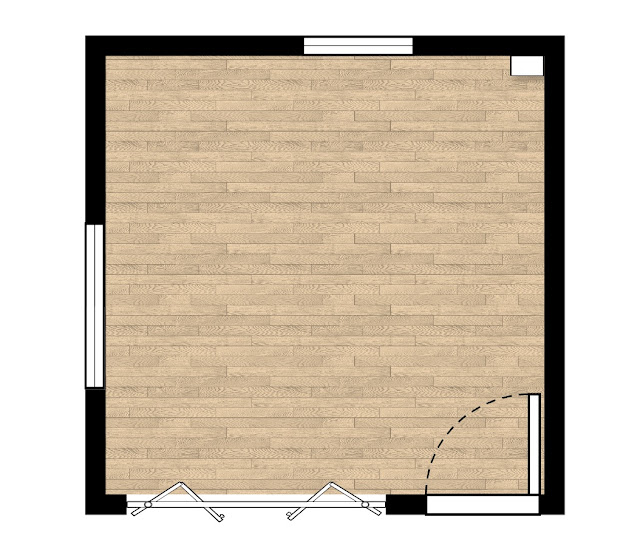
You can see the window and door locations, the width of the bifold doors, and the small wall bump out in the top right corner of the room. With this 2D floor plan, you can proceed to design a room layout. But before you do that, you need to know how your room functions, and know what furniture is going into the room.
2. Determine Your Functional Needs
Every space, from a kitchen to a closet, has a function. Good design is built on satisfying functional needs. What needs or tasks does your room fulfill? What is the role of this room?
Two things you should also consider: You want to think about what currently doesn’t work in the room and also any new functions this room can perform. Can the room be more multifunctional? The planning stage is when you easily build the design to suit your needs.
For our guest bedroom, the needs were simple:
- To provide sleeping room for guests
- To store clothing and linens
- To provide a small sitting/reading area
- To be well lit and a usable room in our house
3. Identify Your Furniture
Once you’ve determined your functional needs, you can identify what furniture is needed to help fulfill those functions.
In our bedroom, we were able to eliminate the existing dresser by putting drawers into the closet. Taking into account this new free floor space, we wanted to bring the following into the room:
- the existing Double bed
- a side table
- a desk or console
- an armchair for additional seating
- a rug
Using the Room Planner, I identified different bedroom layout options. It’s easy to design a room layout using free online tools like this. Simply pull different objects into the room and move them around. Change the dimensions of the objects if you can to approximate the “real life” furniture you’re using.
A room layout will help you identify different ways you can arrange furniture . It gives you an idea of what feels cramped or spacious, what looks good and what looks awkward. In a small space, every inch counts so you’ll want to think through your floor plan, Most importantly, it gives you a sense of scale.
How to Create a Room in 3D Online for Free
Scale is one of the hardest things to assess in design. It refers to the size of an object or space in relation to the human body. Scale also considers how the objects relate to one another in the same room. Essentially, scale means looking at your space in three dimensions or 3D.
To help with scale, you can also draw a rendering. This can be an elevation (or forward facing view), like this one we did for our old master bedroom showing the panelled accent wall. Sean created this plan using an architectural program, CAD:
You can also create a hand-drawn rendering. To do this, take a photo of the existing space, print it out, and then lay tracing paper on top to draw a rendering of the new space. It will help you see what things will look like in 3D.
Another option is SketchUp, a 3D modelling software. They have a free version which will allow you to design a room online in 3D for free, but beware, there is quite a steep learning curve with SketchUp.
4. Create a Moodboard or Design Scheme
When people think of a “design plan”, this is the step that most people think of. How things look in turn impacts how they feel. The visual scheme of a room is the first thing you encounter when you enter a space so it’s no wonder that this part in the process gets all the attention. But how do you create a moodboard? Here’s three things you can do to pull your design scheme together.
Create A Virtual Inspiration Board on Pinterest:
Use Pinterest to gather ideas that show a finished look you are inspired by. Examine the images you’ve gathered and ask yourself what exactly it is in the image that you like? Is there a specific element, colour, or product? Usually, you’ll start to see some commonalities in the images you save and those are the elements that you can replicate in your own room.
Put Together A Pin Board
Using a pin board can help you visualize how things will work together. Pin up fabric samples, paint chips, and images torn out of magazines that inspire you. If you have furniture spec sheets, floor samples or tile samples, gather them together in one spot.
Create A Moodboard For Free in Keynote
A Keynote Moodboard is the tool I tend to use most. If you have a Mac computer, the Keynote program comes free installed. I’ve talked in depth about how to create a moodboard in keynote on this post. I’m re-sharing the video here as it’s really easy to follow:
You can easily swap furniture pieces in and out on your Keynote moodboard. Here’s a few of the design schemes I created for this room:
These designs aren’t drastically different from one another. Change out the rug here, try a different desk there. The possibilities are limitless. Selecting the individual pieces can be daunting and you might be wondering
in what order do you decorate a room.
Here’s the order I typically use:
Existing Furniture: Rarely will I buy everything new for a room. Typically, I’ll have existing furniture, art or decor pieces that I’ll want to reuse. In this case, the bed, side table, some bed linens, printed curtains, and rug are all things I already own. To keep this room budget friendly, I’d like to reuse what I can, but I’m not opposed to switching some of them out for newer items if the design works better.
Hard Goods: Furniture pieces like sofas and chairs, desks, beds, and tables tend to be the largest pieces in any room. They are an important part of the design scheme so spend time thinking about their shape, colour, and texture. These hard goods convey your room’s style – is it modern or farmhouse? Is it bold and energetic or muted and calm? The bold
Velvet Swoop Arm Accent Chair in Green from HomePop is a focal point in this space and intentionally livens up what would otherwise be a neutral decorating scheme.
Art: The Berry Branch Botanicals from Rainsford Company are the elements that tie this entire design scheme together. I fell in love with these art pieces and wanted to use their colour palette as inspiration for the room. I was really drawn to the verdant greens and blues and the black frames and you’ll see those colours repeated throughout my mood boards.
Lighting and Hardware: I consider these “metal” elements as one group. You can certainly mix metals in a space but don’t overdo it. In this room, I’m going with a mix of black and gold. The black hardware will tie in with the black metal bed and gold keeps things feeling modern and fresh.
Soft goods and accessories: These elements are the easiest to change and so they fall to the bottom of the priority list. Use your soft goods and accessories to complement your larger elements and colour scheme.
In the end, there is no right or wrong to a room’s design. By following these steps though, you will end up with a room that makes best use of the space, meets your functional needs, and whose design reflects your style.
If you’d like more decorating know-how, design inspiration and style tips sent to your mailbox, signup for my weekly newsletter:
.formkit-form[data-uid=”8fd6c67e27″] *box-sizing:border-box;.formkit-form[data-uid=”8fd6c67e27″]-webkit-font-smoothing:antialiased;-moz-osx-font-smoothing:grayscale;.formkit-form[data-uid=”8fd6c67e27″] legendborder:none;font-size:inherit;margin-bottom:10px;padding:0;position:relative;display:table;.formkit-form[data-uid=”8fd6c67e27″] fieldsetborder:0;padding:0.01em 0 0 0;margin:0;min-width:0;.formkit-form[data-uid=”8fd6c67e27″] body:not(:-moz-handler-blocked) fieldsetdisplay:table-cell;.formkit-form[data-uid=”8fd6c67e27″] h1,.formkit-form[data-uid=”8fd6c67e27″] h2,.formkit-form[data-uid=”8fd6c67e27″] h3,.formkit-form[data-uid=”8fd6c67e27″] h4,.formkit-form[data-uid=”8fd6c67e27″] h5,.formkit-form[data-uid=”8fd6c67e27″] h6color:inherit;font-size:inherit;font-weight:inherit;.formkit-form[data-uid=”8fd6c67e27″] pcolor:inherit;font-size:inherit;font-weight:inherit;.formkit-form[data-uid=”8fd6c67e27″][data-format=”modal”]display:none;.formkit-form[data-uid=”8fd6c67e27″][data-format=”slide in”]display:none;.formkit-form[data-uid=”8fd6c67e27″] .formkit-input,.formkit-form[data-uid=”8fd6c67e27″] .formkit-select,.formkit-form[data-uid=”8fd6c67e27″] .formkit-checkboxeswidth:100%;.formkit-form[data-uid=”8fd6c67e27″] .formkit-button,.formkit-form[data-uid=”8fd6c67e27″] .formkit-submitborder:0;border-radius:5px;color:#ffffff;cursor:pointer;display:inline-block;text-align:center;font-size:15px;font-weight:500;cursor:pointer;margin-bottom:15px;overflow:hidden;padding:0;position:relative;vertical-align:middle;.formkit-form[data-uid=”8fd6c67e27″] .formkit-button:hover,.formkit-form[data-uid=”8fd6c67e27″] .formkit-submit:hover,.formkit-form[data-uid=”8fd6c67e27″] .formkit-button:focus,.formkit-form[data-uid=”8fd6c67e27″] .formkit-submit:focusoutline:none;.formkit-form[data-uid=”8fd6c67e27″] .formkit-button:hover > span,.formkit-form[data-uid=”8fd6c67e27″] .formkit-submit:hover > span,.formkit-form[data-uid=”8fd6c67e27″] .formkit-button:focus > span,.formkit-form[data-uid=”8fd6c67e27″] .formkit-submit:focus > spanbackground-color:rgba(0,0,0,0.1);.formkit-form[data-uid=”8fd6c67e27″] .formkit-button > span,.formkit-form[data-uid=”8fd6c67e27″] .formkit-submit > spandisplay:block;-webkit-transition:all 300ms ease-in-out;transition:all 300ms ease-in-out;padding:12px 24px;.formkit-form[data-uid=”8fd6c67e27″] .formkit-inputbackground:#ffffff;font-size:15px;padding:12px;border:1px solid #e3e3e3;-webkit-flex:1 0 auto;-ms-flex:1 0 auto;flex:1 0 auto;line-height:1.4;margin:0;-webkit-transition:border-color ease-out 300ms;transition:border-color ease-out 300ms;.formkit-form[data-uid=”8fd6c67e27″] .formkit-input:focusoutline:none;border-color:#1677be;-webkit-transition:border-color ease 300ms;transition:border-color ease 300ms;.formkit-form[data-uid=”8fd6c67e27″] .formkit-input::-webkit-input-placeholdercolor:inherit;opacity:0.8;.formkit-form[data-uid=”8fd6c67e27″] .formkit-input::-moz-placeholdercolor:inherit;opacity:0.8;.formkit-form[data-uid=”8fd6c67e27″] .formkit-input:-ms-input-placeholdercolor:inherit;opacity:0.8;.formkit-form[data-uid=”8fd6c67e27″] .formkit-input::placeholdercolor:inherit;opacity:0.8;.formkit-form[data-uid=”8fd6c67e27″] [data-group=”dropdown”]position:relative;display:inline-block;width:100%;.formkit-form[data-uid=”8fd6c67e27″] [data-group=”dropdown”]::beforecontent:””;top:calc(50% – 2.5px);right:10px;position:absolute;pointer-events:none;border-color:#4f4f4f transparent transparent transparent;border-style:solid;border-width:6px 6px 0 6px;height:0;width:0;z-index:999;.formkit-form[data-uid=”8fd6c67e27″] [data-group=”dropdown”] selectheight:auto;width:100%;cursor:pointer;color:#333333;line-height:1.4;margin-bottom:0;padding:0 6px;-webkit-appearance:none;-moz-appearance:none;appearance:none;font-size:15px;padding:12px;padding-right:25px;border:1px solid #e3e3e3;background:#ffffff;.formkit-form[data-uid=”8fd6c67e27″] [data-group=”dropdown”] select:focusoutline:none;.formkit-form[data-uid=”8fd6c67e27″] [data-group=”checkboxes”]text-align:left;margin:0;.formkit-form[data-uid=”8fd6c67e27″] [data-group=”checkboxes”] [data-group=”checkbox”]margin-bottom:10px;.formkit-form[data-uid=”8fd6c67e27″] [data-group=”checkboxes”] [data-group=”checkbox”] *cursor:pointer;.formkit-form[data-uid=”8fd6c67e27″] [data-group=”checkboxes”] [data-group=”checkbox”]:last-of-typemargin-bottom:0;.formkit-form[data-uid=”8fd6c67e27″] [data-group=”checkboxes”] [data-group=”checkbox”] input[type=”checkbox”]display:none;.formkit-form[data-uid=”8fd6c67e27″] [data-group=”checkboxes”] [data-group=”checkbox”] input[type=”checkbox”] + label::aftercontent:none;.formkit-form[data-uid=”8fd6c67e27″] [data-group=”checkboxes”] [data-group=”checkbox”] input[type=”checkbox”]:checked + label::afterborder-color:#ffffff;content:””;.formkit-form[data-uid=”8fd6c67e27″] [data-group=”checkboxes”] [data-group=”checkbox”] input[type=”checkbox”]:checked + label::beforebackground:#10bf7a;border-color:#10bf7a;.formkit-form[data-uid=”8fd6c67e27″] [data-group=”checkboxes”] [data-group=”checkbox”] labelposition:relative;display:inline-block;padding-left:28px;.formkit-form[data-uid=”8fd6c67e27″] [data-group=”checkboxes”] [data-group=”checkbox”] label::before,.formkit-form[data-uid=”8fd6c67e27″] [data-group=”checkboxes”] [data-group=”checkbox”] label::afterposition:absolute;content:””;display:inline-block;.formkit-form[data-uid=”8fd6c67e27″] [data-group=”checkboxes”] [data-group=”checkbox”] label::beforeheight:16px;width:16px;border:1px solid #e3e3e3;background:#ffffff;left:0px;top:3px;.formkit-form[data-uid=”8fd6c67e27″] [data-group=”checkboxes”] [data-group=”checkbox”] label::afterheight:4px;width:8px;border-left:2px solid #4d4d4d;border-bottom:2px solid #4d4d4d;-webkit-transform:rotate(-45deg);-ms-transform:rotate(-45deg);transform:rotate(-45deg);left:4px;top:8px;.formkit-form[data-uid=”8fd6c67e27″] .formkit-alertbackground:#f9fafb;border:1px solid #e3e3e3;border-radius:5px;-webkit-flex:1 0 auto;-ms-flex:1 0 auto;flex:1 0 auto;list-style:none;margin:25px auto;padding:12px;text-align:center;width:100%;.formkit-form[data-uid=”8fd6c67e27″] .formkit-alert:emptydisplay:none;.formkit-form[data-uid=”8fd6c67e27″] .formkit-alert-successbackground:#d3fbeb;border-color:#10bf7a;color:#0c905c;.formkit-form[data-uid=”8fd6c67e27″] .formkit-alert-errorbackground:#fde8e2;border-color:#f2643b;color:#ea4110;.formkit-form[data-uid=”8fd6c67e27″] .formkit-spinnerdisplay:-webkit-box;display:-webkit-flex;display:-ms-flexbox;display:flex;height:0px;width:0px;margin:0 auto;position:absolute;top:0;left:0;right:0;width:0px;overflow:hidden;text-align:center;-webkit-transition:all 300ms ease-in-out;transition:all 300ms ease-in-out;.formkit-form[data-uid=”8fd6c67e27″] .formkit-spinner > divmargin:auto;width:12px;height:12px;background-color:#fff;opacity:0.3;border-radius:100%;display:inline-block;-webkit-animation:formkit-bouncedelay-formkit-form-data-uid-8fd6c67e27- 1.4s infinite ease-in-out both;animation:formkit-bouncedelay-formkit-form-data-uid-8fd6c67e27- 1.4s infinite ease-in-out both;.formkit-form[data-uid=”8fd6c67e27″] .formkit-spinner > div:nth-child(1)-webkit-animation-delay:-0.32s;animation-delay:-0.32s;.formkit-form[data-uid=”8fd6c67e27″] .formkit-spinner > div:nth-child(2)-webkit-animation-delay:-0.16s;animation-delay:-0.16s;.formkit-form[data-uid=”8fd6c67e27″] .formkit-submit[data-active] .formkit-spinneropacity:1;height:100%;width:50px;.formkit-form[data-uid=”8fd6c67e27″] .formkit-submit[data-active] .formkit-spinner ~ spanopacity:0;.formkit-form[data-uid=”8fd6c67e27″] .formkit-powered-by[data-active=”false”]opacity:0.35;@-webkit-keyframes formkit-bouncedelay-formkit-form-data-uid-8fd6c67e27-0%,80%,100%-webkit-transform:scale(0);-ms-transform:scale(0);transform:scale(0);40%-webkit-transform:scale(1);-ms-transform:scale(1);transform:scale(1);@keyframes formkit-bouncedelay-formkit-form-data-uid-8fd6c67e27-0%,80%,100%-webkit-transform:scale(0);-ms-transform:scale(0);transform:scale(0);40%-webkit-transform:scale(1);-ms-transform:scale(1);transform:scale(1); .formkit-form[data-uid=”8fd6c67e27″]max-width:700px;.formkit-form[data-uid=”8fd6c67e27″] [data-style=”clean”]width:100%;.formkit-form[data-uid=”8fd6c67e27″] .formkit-fieldsdisplay:-webkit-box;display:-webkit-flex;display:-ms-flexbox;display:flex;-webkit-flex-wrap:wrap;-ms-flex-wrap:wrap;flex-wrap:wrap;margin:0 auto;.formkit-form[data-uid=”8fd6c67e27″] .formkit-field,.formkit-form[data-uid=”8fd6c67e27″] .formkit-submitmargin:0 0 15px 0;-webkit-flex:1 0 100%;-ms-flex:1 0 100%;flex:1 0 100%;.formkit-form[data-uid=”8fd6c67e27″] .formkit-powered-bycolor:#7d7d7d;display:block;font-size:12px;margin:0;text-align:center;.formkit-form[data-uid=”8fd6c67e27″][min-width~=”700″] [data-style=”clean”],.formkit-form[data-uid=”8fd6c67e27″][min-width~=”800″] [data-style=”clean”]padding:10px;.formkit-form[data-uid=”8fd6c67e27″][min-width~=”700″] .formkit-fields[data-stacked=”false”],.formkit-form[data-uid=”8fd6c67e27″][min-width~=”800″] .formkit-fields[data-stacked=”false”]margin-left:-5px;margin-right:-5px;.formkit-form[data-uid=”8fd6c67e27″][min-width~=”700″] .formkit-fields[data-stacked=”false”] .formkit-field,.formkit-form[data-uid=”8fd6c67e27″][min-width~=”800″] .formkit-fields[data-stacked=”false”] .formkit-field,.formkit-form[data-uid=”8fd6c67e27″][min-width~=”700″] .formkit-fields[data-stacked=”false”] .formkit-submit,.formkit-form[data-uid=”8fd6c67e27″][min-width~=”800″] .formkit-fields[data-stacked=”false”] .formkit-submitmargin:0 5px 15px 5px;.formkit-form[data-uid=”8fd6c67e27″][min-width~=”700″] .formkit-fields[data-stacked=”false”] .formkit-field,.formkit-form[data-uid=”8fd6c67e27″][min-width~=”800″] .formkit-fields[data-stacked=”false”] .formkit-field-webkit-flex:100 1 auto;-ms-flex:100 1 auto;flex:100 1 auto;.formkit-form[data-uid=”8fd6c67e27″][min-width~=”700″] .formkit-fields[data-stacked=”false”] .formkit-submit,.formkit-form[data-uid=”8fd6c67e27″][min-width~=”800″] .formkit-fields[data-stacked=”false”] .formkit-submit-webkit-flex:1 1 auto;-ms-flex:1 1 auto;flex:1 1 auto;
Join me again next week where I talk about the next phase, the Work Breakdown and Timeline. For now, hop over to the
One Room Challenge blog and see all of the other inspiring Guest Participant projects.
